Material Selection Guide
With Hundreds of thousands of materials to choose from we understand the daunting challenges of material selection. Caliber employs a methodical approach to helping you achieve targeted material performance parameters within your budget constraints. Some of the information below may help you understand some of the general considerations and guidelines in material consideration.
- Tensile Strength
- Impact Strength
- Flexural Modules (Bending Stiffness)
- Temperature Resistance
- Chemical Resistance
- Environmental Resistance (UV)
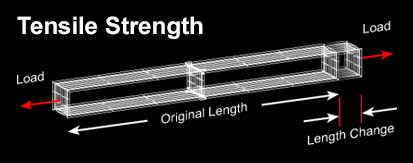
Tensile Strength
Tensile strength is the maximum stress that a material can withstand while being stretched or pulled before necking, which is when the specimen’s cross-section starts to significantly stretch. Tensile strength is the opposite of compressive strength and the values can be quite different. Measurements are taken in both Ultimate (brake) and Yield. Tensile strengths are rarely used in the selection of soft materials, but they are important in brittle and ridged materials.
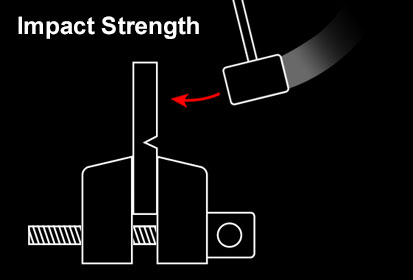
Impact Strength
Defines the “toughness” of material. A material’s toughness is a factor of its ability to absorb energy during plastic deformation. Brittle materials have low toughness as a result of the small amount of plastic deformation that they can endure. The impact value of a material can also change with temperature. Generally, at lower temperatures, the impact strength of a material is decreased. The size of the specimen may also affect the value of the Izod impact test because it may allow a different number of imperfections in the material, which can act as stress risers and lower the impact strength. An arm held at a specific height (constant potential energy) is released. The arm hits the sample and breaks it. From the energy absorbed by the sample, its impact strength is determined. The North American standard for Izod Impact testing of plastics is ASTM D256
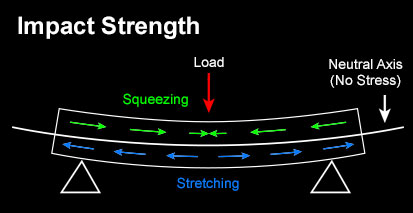
Flexural Strength
Mechanical parameter for brittle material is defined as a material’s ability to resist deformation under load. The transverse bending test is most frequently employed, in which a rod specimen having either a circular or rectangular cross-section is bent until fracture using a three point flexural test technique. The flexural strength represents the highest stress experienced within the material at its moment of rupture.
Durometer
Durometer is one measure of the hardness of a material. Hardness may be defined as a material’s resistance to permanent indentation. The term durometer is often used to refer to the measurement, as well as the instrument itself. Durometer is typically used as a measure of hardness in plastics and helps us define ductility requirements for your part. Measurements are taken with ASTM D2240 type A and type D scales.
Chemical Resistance
Chemical Resistance of a material or surface can be determined in compliance with ISO 2812 Paints and varnishes – Determination of resistance to liquids – Part 1: Immersion in liquids other than water (ISO 2812-1:2007[1]).
Environmental Resistance
UV attack by sunlight can be prevented by adding anti-UV additive to the polymer when selecting the correct plastic, color and understanding its life-cycle expectations prior to injection molding. UV Stabilizers in plastics usually act by absorbing the UV radiation preferentially, and dissipating the energy as low level heat. Today we have many 5 and 7 year UV guarantees pigment packages that will provide the best UV protection possible. With modern testing we can it is possible to simulate 63 years of natural UV radiation exposure on a test device in a single year.
Additional Additive Options
Consider options that can be used to help you optimize your parts.
Lubrication: additives that increase or decrease “Slip” or Coefficient of Friction
Foaming: consider a foaming agent that will lighten your part, reduce cycle time and increase strength.
Strength: increase strength and optimize your parts with glass or carbon fibers. Dramatically increase strength with minimal cost.